Castheon has expertise in the development of unique materials that are ideally suited for use in our suite of additive machines with a proven track record of success in developing materials that meet the specific needs of our customers across various industries. Our team of experts has extensive knowledge and experience in material science, which enables us to select the best materials for each project based on specific requirements. Castheon’s focus on material development and selection is a crucial component of our commitment to providing our customers with the best possible results.
Materials
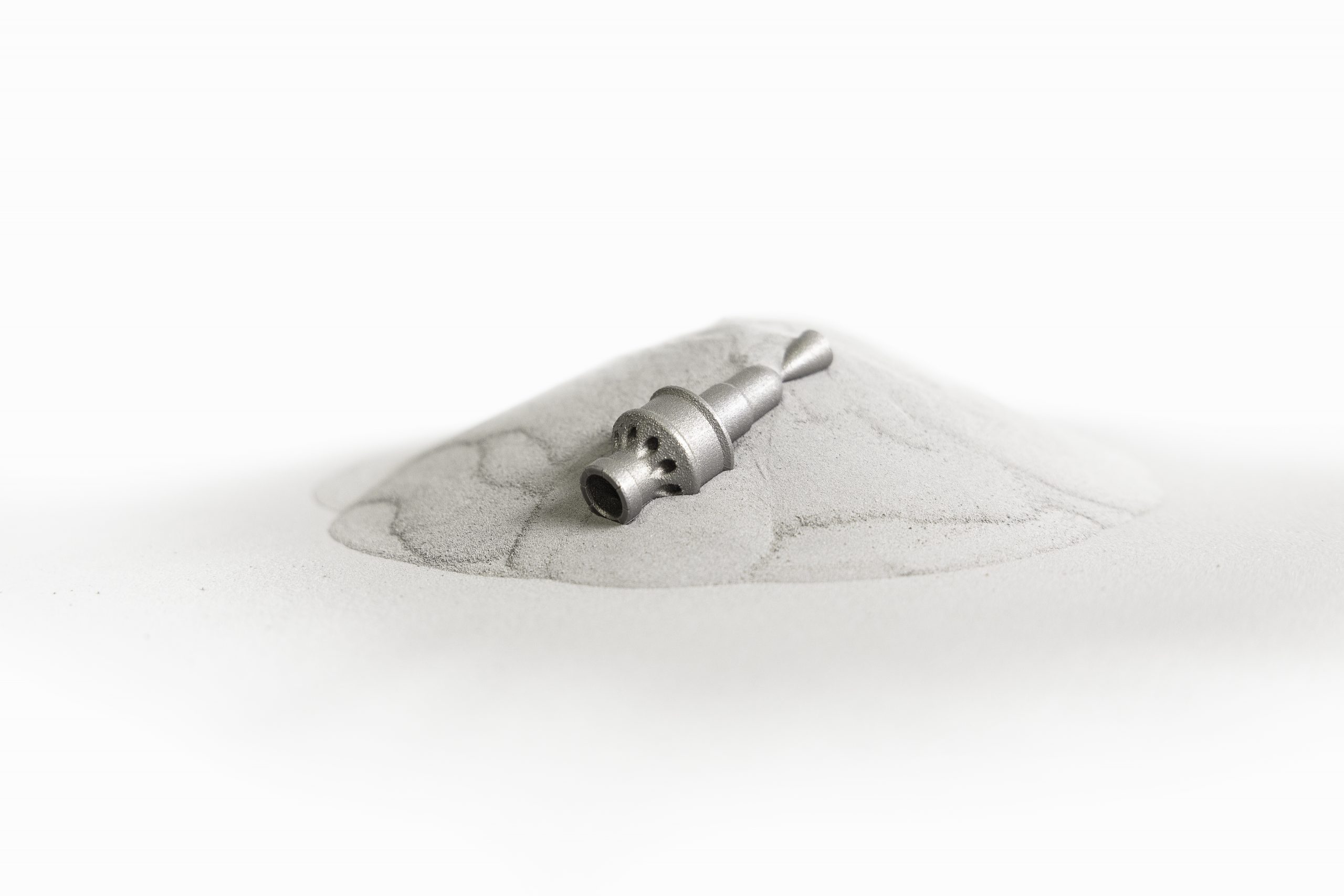
Refractory Metals
Refractory metals, particularly niobium alloys, are gaining popularity in the aerospace industry due to their high strength, low weight, and excellent corrosion and wear resistance. However, these metals can be difficult to process and fabricate due to their high melting points and brittleness, limiting their use in some applications. Dr. Youping Gao and his team at Castheon have developed new ways to 3D print refractory metal components for hypersonic applications and the military and defense industry, providing precise control over material properties and microstructure while enabling the creation of complex geometries and designs. This breakthrough technology opens up new possibilities for the use of refractory metals in aerospace and defense applications, paving the way for the next generation of hypersonic missiles and defense systems.
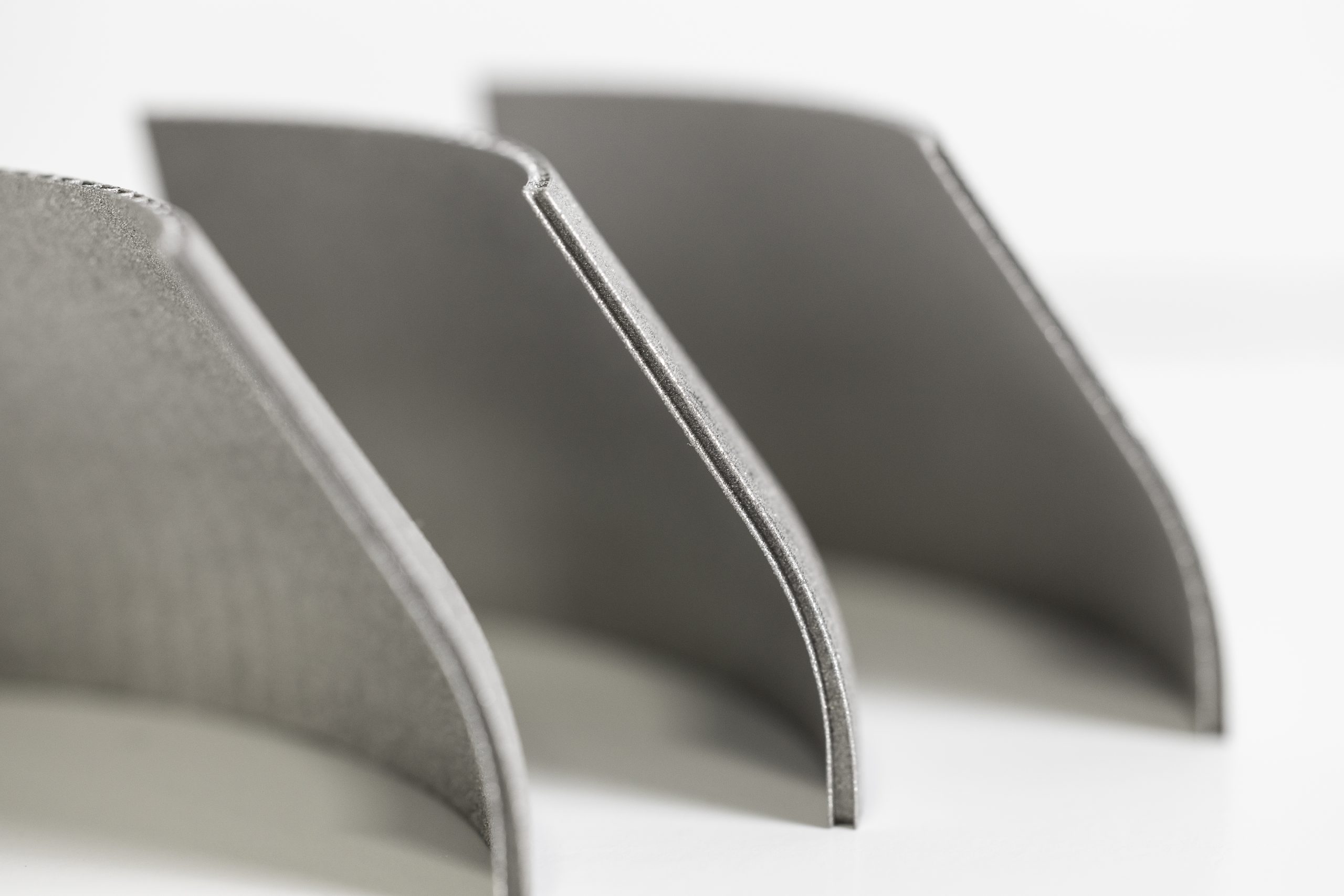
Niobium C103
Dr. Gao’s groundbreaking research has revolutionized metallurgical control in refractory metal additive manufacturing. Castheon’s Super C103, a high-performance niobium alloy perfect for hypersonic and satellite propulsion applications, was developed with material parameters on a Concept Laser M2 machine. Niobium is a challenging material to print, but Dr. Gao’s parameters have resulted in superior mechanical and thermal properties compared to conventionally wrought niobium. The technology has already proven successful in producing RCS thrusters for spacecraft customers and has the potential to significantly reduce costs and increase design flexibility. Learn more about what makes Niobium unique for hypersonic applications:
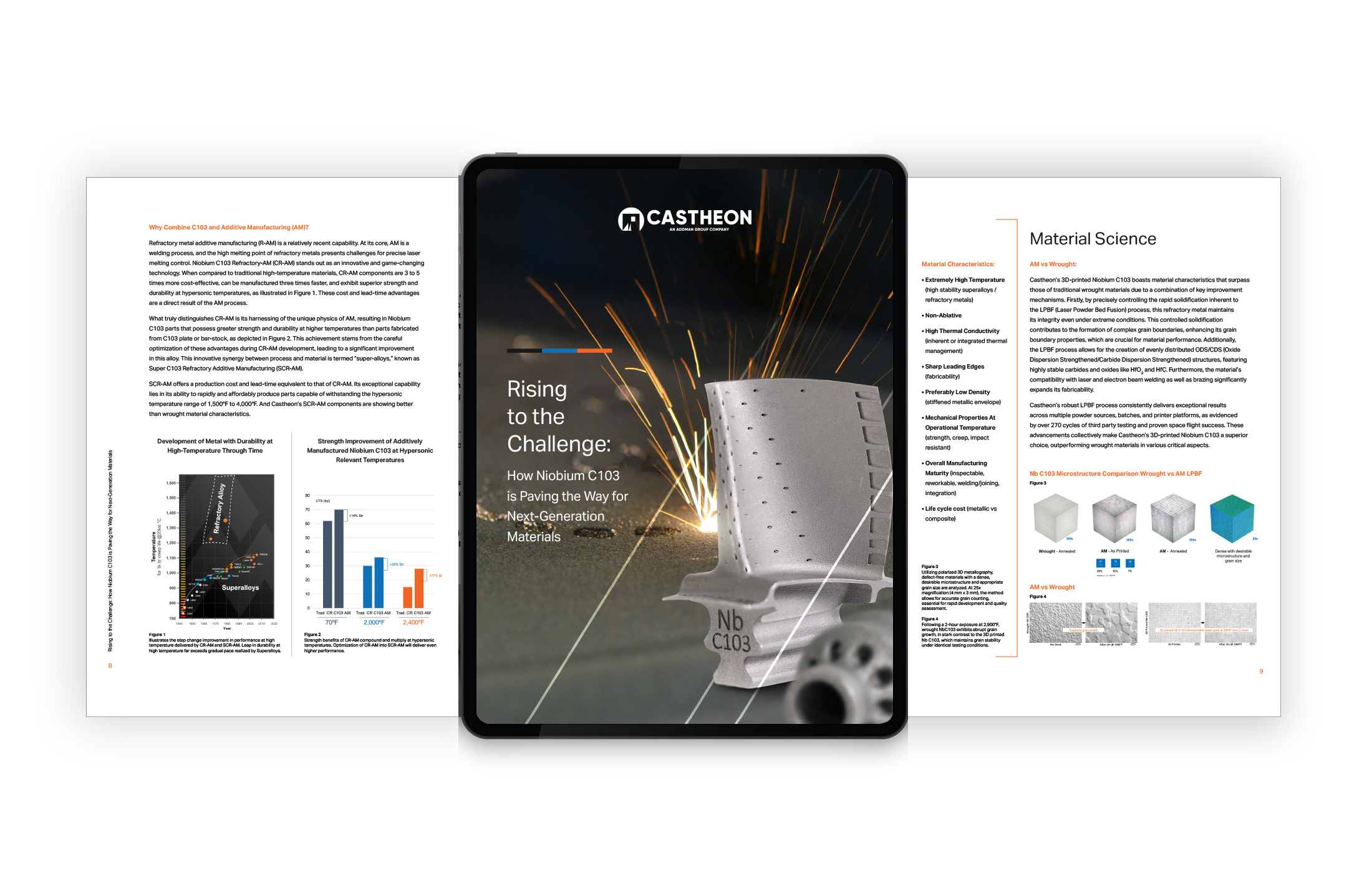
How Niobium C103 is Paving the Way for Next-Generation Materials
Embark on an aerospace journey like never before. Our eBook unveils the incredible story of Niobium C103—a superalloy that has earned its wings in the aerospace industry. Dive into the historical narrative, understand its unmatched properties, and witness its transformational role in aviation. Ready to soar? Download the eBook now.
Super C103™
Castheon advances the field of additive manufacturing with its proprietary and patented technique focused on Super C103 components. Central to this innovative process is the strategic distribution of oxide and nitride dispersoids within Niobium C103 powder, executed during the Direct Metal Laser Sintering (DMLS) phase. This method significantly boosts the structural integrity of the material, designed to withstand high temperatures. The outcome is robust components that offer exceptional strength and durability, making them ideal for critical applications that require superior performance in extreme conditions.
Inconel
Inconel 718 and Inconel 625 are nickel-based alloys with exceptional high-temperature strength and resistance to corrosion. Inconel 718 offers excellent tensile and impact strength at temperatures up to 1,400°F and is commonly used in gas turbine engines, aerospace components, and cryogenic tanks. Inconel 625 offers exceptional corrosion resistance in various aggressive environments and is commonly used in chemical processing, marine engineering, and oil and gas applications. Both alloys are known for their ability to maintain their properties even in high-stress and high-temperature environments, making them ideal choices for demanding industrial applications.
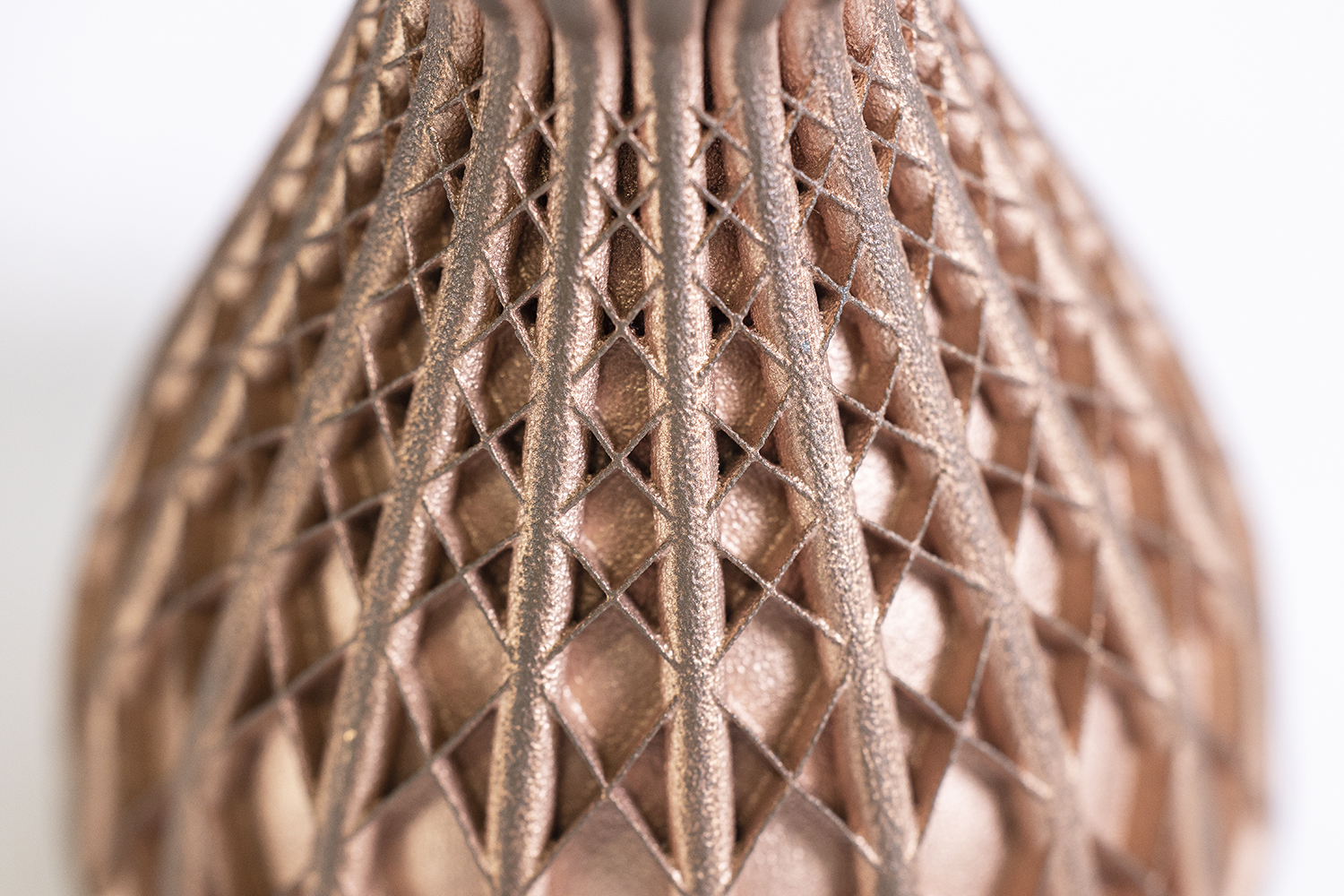
CuCr
CuCr, or copper-chromium, is a high-strength copper alloy that offers excellent electrical and thermal conductivity, as well as corrosion resistance. It is commonly used in electrical and electronic applications, as well as in the aerospace and automotive industries due to its high strength and wear resistance. The alloy can be easily machined and formed, making it an ideal choice for applications where complex shapes or precise tolerances are required. Additionally, CuCr has a low coefficient of thermal expansion, which makes it an excellent choice for applications that require stability over a wide range of temperatures. Overall, CuCr is a versatile and reliable material that offers a unique combination of strength, conductivity, and resistance to wear and corrosion.
GRCop-84/42
GRCop-84 and GRCop-42 are high-performance copper alloys that are specifically designed for aerospace applications. GRCop-84 offers exceptional thermal conductivity and mechanical strength, with a thermal conductivity of up to 380 W/mK and a tensile strength of up to 310 MPa. GRCop-42, on the other hand, offers high thermal conductivity and electrical conductivity, with a thermal conductivity of up to 400 W/mK and an electrical conductivity of up to 90% IACS. Both alloys have excellent resistance to thermal fatigue and are capable of withstanding high temperatures and harsh environments, making them ideal for use in rocket engines, thrusters, and other high-performance aerospace applications. Additionally, their high thermal conductivity makes them an excellent choice for heat transfer applications, such as heat exchangers and cooling systems.
CPTi
CPTi, or Commercially Pure Titanium, is a grade of titanium with excellent corrosion resistance and biocompatibility, making it ideal for use in medical implants and devices. It is a non-alloyed, alpha titanium with a high level of purity, typically containing over 99% titanium. CPTi also offers excellent strength-to-weight ratio and ductility, making it suitable for a range of industrial applications such as aerospace, marine, and chemical processing. The material is relatively easy to form and weld, making it a popular choice for manufacturing components that require a high level of corrosion resistance and strength, such as tanks, heat exchangers, and pipelines.
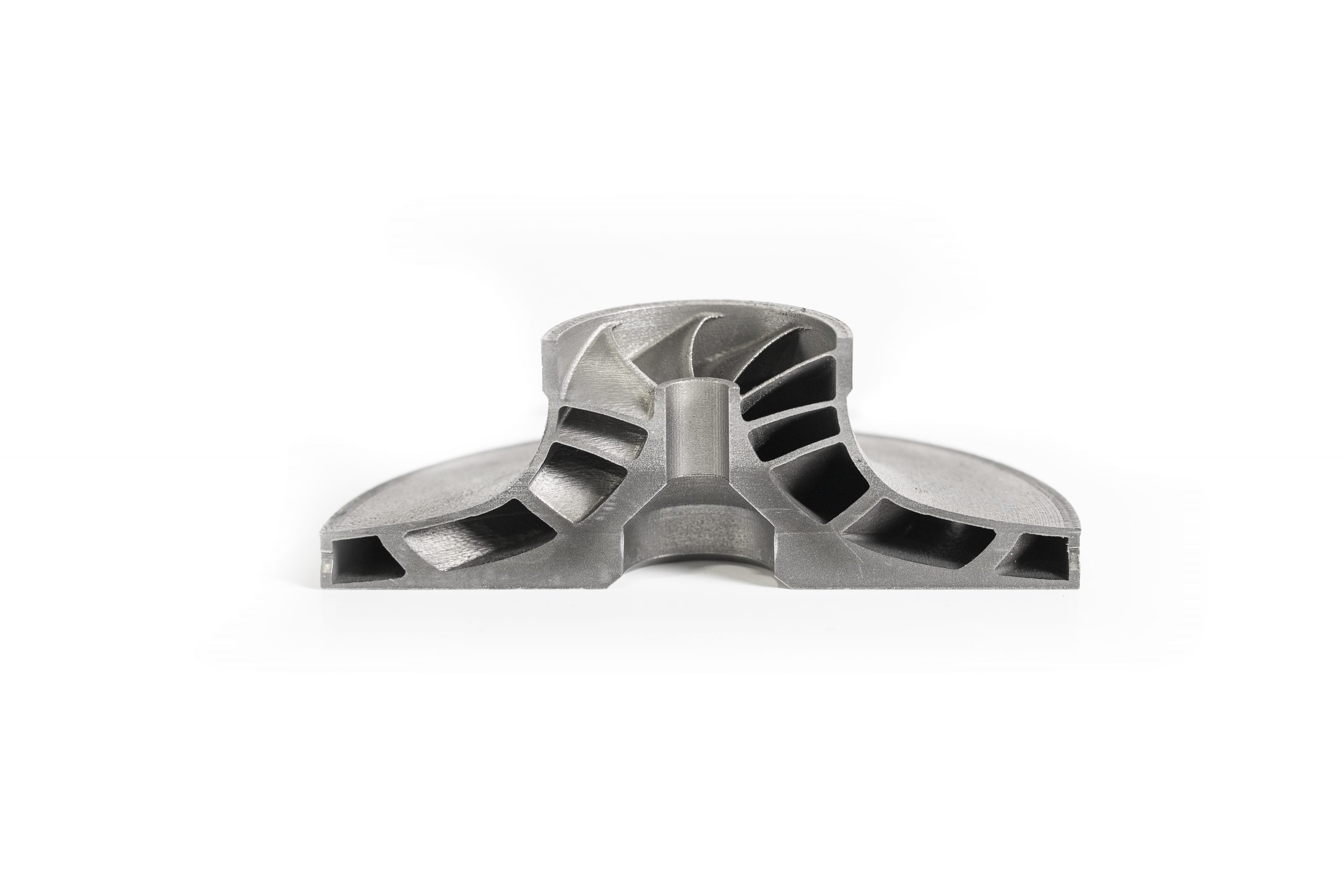
Ti6Al4V Gr 5, 23
Ti6Al4V, also known as Grade 5 titanium, is a popular titanium alloy due to its excellent strength-to-weight ratio, high corrosion resistance, and biocompatibility. It is commonly used in aerospace, medical, and industrial applications, such as aircraft components, surgical implants, and chemical processing equipment. Ti6Al4V Grade 23, also known as Ti-6-4 ELI (Extra Low Interstitial), is a variant of Ti6Al4V with reduced levels of interstitial elements, making it even more biocompatible and suitable for medical applications. Both alloys can be easily machined and fabricated using conventional methods, and are well-suited for additive manufacturing techniques such as powder bed fusion and directed energy deposition.
Al Alloys
Aluminum alloys are a group of materials that are widely used in various industrial applications due to their unique combination of properties. These alloys are lightweight, corrosion-resistant, and have good thermal and electrical conductivity, making them ideal for aerospace, automotive, and structural applications. The most common aluminum alloy is 6061-T6, which offers a high strength-to-weight ratio and excellent machinability. Another popular alloy is 7075-T6, which is known for its high strength and fatigue resistance. Aluminum alloys can also be enhanced with additional elements such as copper, magnesium, and zinc to improve their mechanical properties. Despite their numerous advantages, aluminum alloys can be susceptible to stress corrosion cracking and have lower melting points compared to other metals, which can limit their use in high-temperature applications.